MAKING THE PERFECT HAY BALE
For Staffordshire farmer David Wilkes, making hay bales that are consistent in size, density and quality is an on-going quest and an essential part of the CWP Wilkes business.
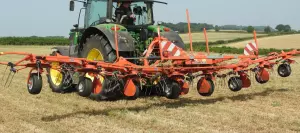
Small hay bales from around 200 acres of grassland at 500-acre Checkhill Farm are made annually, with the majority being sold into the local equestrian market.
Demand is high, as are expectations of consistency, so producing year-in, year-out, whatever the weather, does come with its fair share of pressures.
“Nothing can ever be 100% guaranteed, but we’ve developed a system that removes a lot of the risks and is relatively efficient,” says David. “We try to keep the hay meadows as weed free as we can, so that we are starting with a relatively clean sward. We are then mowing as early in the season as we can and aim to make the hay as quickly as possible. We do have the advantage of light, free-draining land, but there’s no substitute for having machinery that’s effective and most of all reliable.”
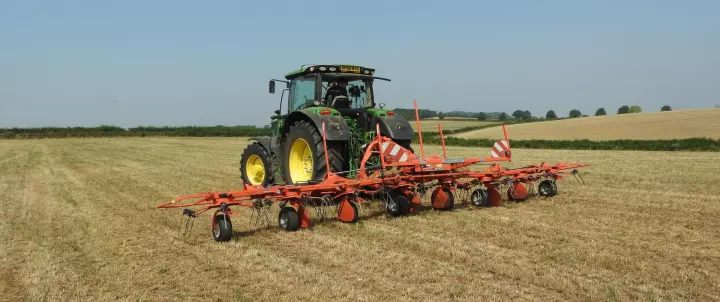
Checkhill Farm, near Kinver, runs a sizeable horse livery business alongside grassland for hay and haylage production and around 200 acres of arable cropping including triticale, winter oilseed rape and spring barley. A significant area of grassland is dedicated to horse grazing, and around 90 acres of the farm is within a conservation scheme due to areas of archaeological interest and is limited to only growing specific grassland species.
Grass for hay is cut with a three-metre trailed mower conditioner into windrows, with the adjustable steel flail conditioning unit helping to take up to a day out of the drying process. The crop is then tedded out, initially slowly and carefully to achieve the best possible spread. Tedding is then repeated as often as is required to achieve optimum drying before the grass is rowed up for baling.
Even tedding of the grass is a key element, according to David, so investment in a new Kuhn GF 8712 Gyrotedder in 2019 was done after a great deal of consideration.
“We looked at all the options and then decided to replace our existing Kuhn tedder with the newer model,” says David. “We need a strong and reliable machine as it’ll be expected to do a lot of work, and last us at least five years. We are tedding each crop as many as four times and possibly twice in a day, and timeliness can be critical, so being able to do a quality job whilst covering 15 – 16 acres an hour is important.
“The key difference with this newer model is the Headland Lift Control feature, which ensures all the rotors are lifted fully out of the crop at the headlands, thereby ensuring these areas remain evenly spread and are not over tedded. It is easy to pre-set the rotor height and speed, so operating at the headlands is effectively automated and the whole operation is a lot easier. The tedder is also very quick to fold into its transport position and is very compact when folded, and that’s important as we do need to move between fields quite a lot.”
David has also noted greater overall stability in work, better alignment with the tractor, improved protection of the driveline and an increase in the number of greasing points on the machine.
The tedder has also been chosen for its compatibility with a twin-rotor rake, which is run at its narrowest setting to ensure four runs for every one run with the tedder. With this arrangement, the crop is always running the same way and that helps to create consistent windrows for the baler.
David uses a modern small baler with a moisture sensor linked to an applicator that applies a forage preservative when the crop is wetter than the optimum for the best quality hay. This ensures that quality is maintained even when conditions are not ideal.
He also uses a stroke counter that is linked to the tractor to ensure bales are of a consistent length and density. This is important for the efficient operation of the Bale Bandit that stacks and binds the bales into easily transportable and stackable blocks.
“We’re aiming for bales of around 14% moisture content, with good shape, consistent length and around 18kg in weight,” adds David. “We do have the tools to achieve this, but the whole process is a lot more straightforward if we have a crop that’s been spread and dried evenly and is presented well for the baler.
“Good spells of weather are always welcome, but I believe we’ve developed an efficient system that removes a lot of the risks in making consistent high quality hay in the UK.”
Other News
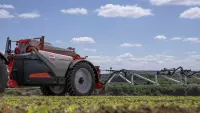
New trailed sprayer KARAN: discover the Efficient Spraying
Discover the new trailed sprayer KARAN, offering tank capacities of 4500, 5200, 6000 & 8000 litres and equipped with steel and aluminium boo...

Explore our latest innovations in crop care
